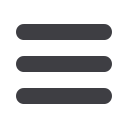
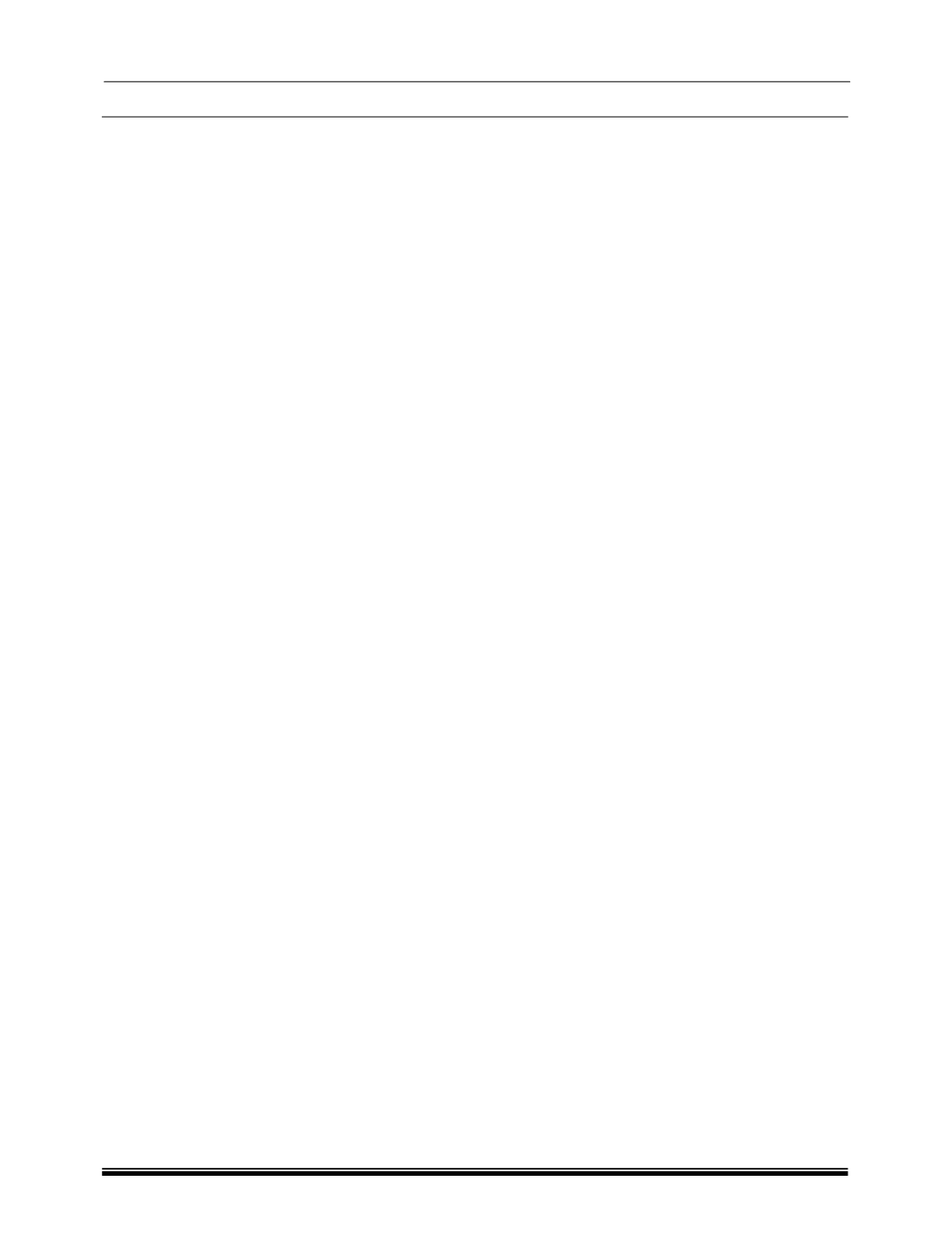
1.05L REVOTORQ ENGINE
120
Inspection :
A. Cylinder Head :
Checking Cylinder Head Mating Surface :
1.
Using a straight edge and feeler gauge, check
evenness of cylinder head parting surface with
crank case. If unevenness exceeds specified
values, replace cylinder head.
2.
Permissible unevenness of cylinder head
mating surface-0.030 mm
(Length wise).
3.
Permissible unevenness of cylinder head
mating surface-0.015 mm
(Cross wise).
Note :
Cylinder head top and bottom surface re-
machining in service is not permitted.
B. Valves :
1.
Check valve leakages by pouring gasoline on
valve head. Gasoline must not seep past valve
seat.
2.
Valves with burnt heads, excessive scoring
and wear on stem should be replaced.
3.
Check valve seat run out with respect to valve
stem. If it exceeds specified limit replace valve.
No attempt should be made to straighten bent
valves.
4.
If valve is free from any other defects except
worn out seat, then only it can be rematched
on valve grinding machine as follows:
Clamp valve on grinding machine jaws as
close as possible to valve head.
Adjust grinding angle on graduated scale to
achieve correct valve seat angle.
Feed valve slowly towards grinding wheel
until wheel just touches valve head.
Grind at low feed until valve seat is just
clean all around.
NOTE:
After grinding, valve head thickness should not be
less than 0.85 mm.
C. Valve Guides :
1.
In case of valve stem sticking in valve guide
bore or Excessive clearance between them,
remove valve guide From cylinder head using
drift (Part No.2868 5890 06 05).
2.
Check the condition of valve guide oil seals.
3.
Check valve guide bore diameter in cylinder
head and if necessary, ream valve guide bore
in cylinder head to next over size.
4.
Install matching size valve guide in cylinder
head using drift (Part No. 2868 5890 06 05)
and spacer (Part No. 2653 5890 06 01).
5.
Fit Valve guide oil seals
D. Valve Seat :
1.
Check valve seat height with respect to
cylinder head mating surface. Replace valve
seat inserts if they are worn out beyond
specified limit.
2.
Cut exhaust and inlet valve seats with a
general 45 deg. cutter.
Note :
Valve seat must be absolutely faultless and
without any chatter marks
3.
If necessary lap the valve seats to a smooth
and even finish by using suitable hand pump
grinder or a lapping paste and valve itself.
4.
Smear valve seat with carbon blue. Install
valve in guide and turn it slowly under axial
pressure.
5.
Contact line on valve seat must be around
entire circumference at equal width.
6.
Distance between narrow diameters of valve
face to contact line should be minimum 0.5
mm.
7.
Check for leakages through valve seat by
pouring gasoline on valve head. Gasoline must
not seep past valve seat.
E. Valve Seat Insert :
1.
For removing valve seat inserts from cylinder
head use suitable boring machine. Bore old
insert thin (About 0.5 mm thickness) and then
pry it out.
2.
Alternatively use a suitable turning tool to cut
an annular groove into valve seat insert and
then pull it out with a suitable puller. In order to
avoid damaging machined cylinder head
mating surface with crank case, place any soft
protective sheet metal under supports of puller.
3.
Measure valve seat insert bore diameter in
cylinder head.
4.
If boring and prying is done carefully without
damaging valve seat insert bore in cylinder
head, fitment of an oversize valve seat insert
will not be necessary.
5.
Re-machined valve seat insert bore in cylinder
head must be exactly at right angle to cylinder
head mating surface with crank case.
6.
All specified dimensions should be strictly
maintained to ensure proper interference of
valve seat insert in its bore.