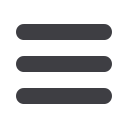
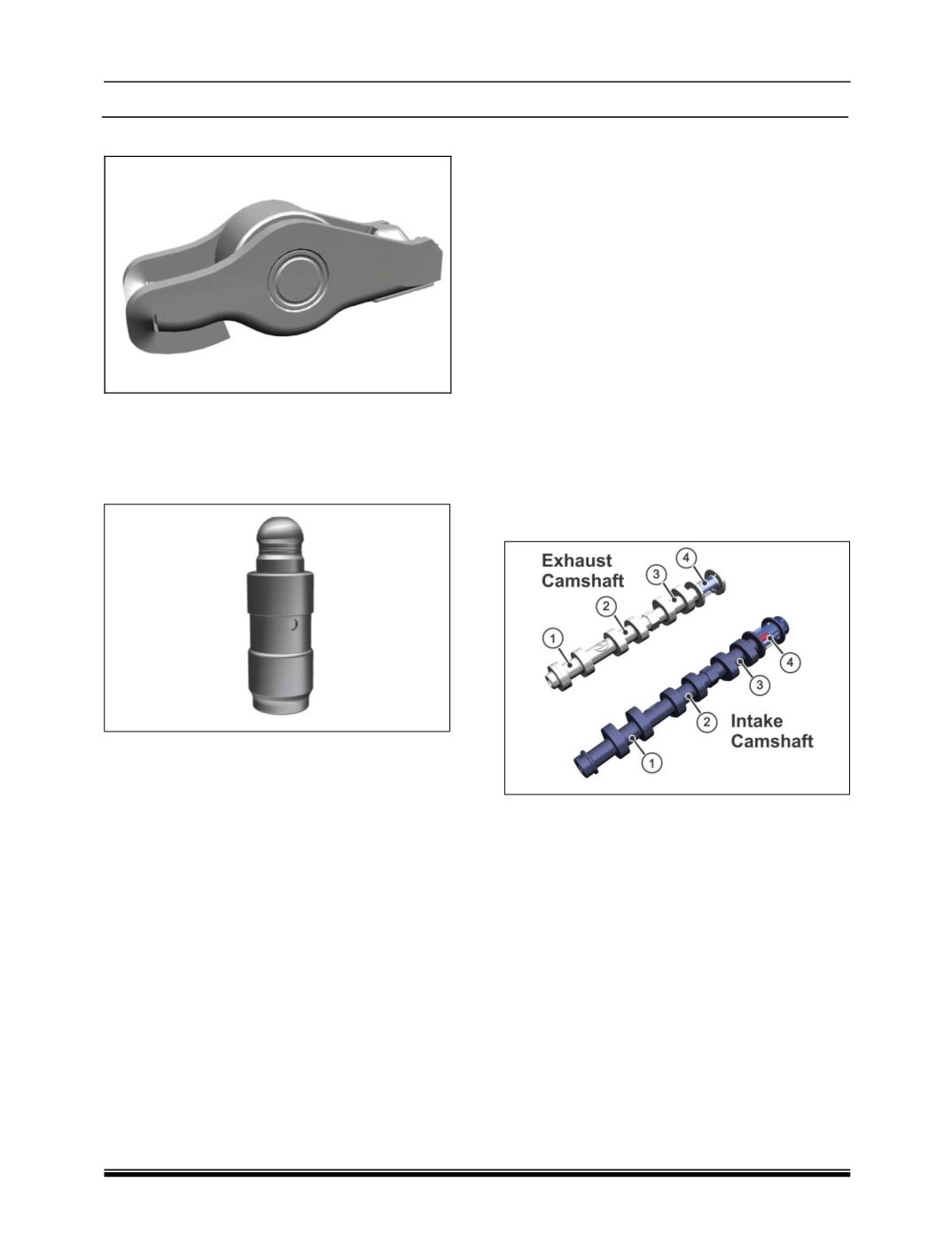
1.2L REVOTRON ENGINE
63
F. Roller Finger Follower :
1. Measure the diameter along several points of
both rocker arm roller. The rocker arm roller
diameter should be Ø17.0 -0.016/-0.027 mm.
Replace the rocker arm if deformed.
G. Hydraulic Lash Adjuster (HLA)
Hydraulic lash adjuster uses Engine oil pressure
for its operation. In case of a freshly assembled
Engine, do not run for a long time; there are
chances of valve train noise / tappet noise
appearing when the engine is started.
HLA noise can be heard as repeated tappet like
noise when engine is running at low idle speed.
Following procedure is recommended to eliminate
the noise.
Raise the Engine speed to 500rpm without
load
(Vehicle stationary)
to bleed the
hydraulic chamber of HLA. The noise should
disappear in15-30seconds.
If the noise still persists, run the engine
further under same condition (no load at 500
RPM) for several minutes. The noise should
disappear in 3 to 30 mins, in few cases.
In a very rare case if the noise is still heard,
the HLA is stuck in compressed position and
has to be replaced
Oil pressure in HLA gallery to be 0.7 bar for
normal functioning.
H. Camshafts (Intake & Exhuast) :
1. Visually inspect the camshaft journals for
signs of overheating and score marks.
2. Visually inspect the camshaft lobes for signs
of excessive wear or score marks.
3. Place camshaft journal 1 and 4 in 'vee blocks'
and check camshaft journal runout on
journals 2, and 3 using a dial indicator. The
maximum journal runout is 0.020 mm
4. Measure the diameter of each of the camshaft
journals. Refer the table for acceptable
journals diameters.
5. Use a bore gauge to measure each of the I.D.
of camshaft bearings. Refer the table for
acceptable bearing diameters.
6. Use a magnetic crack detector to check the
camshaft for cracks.
7. Check the camshaft lobes for proper
hardness. The Rockwell Hardness should be
a minimum of 40 HRC at 3mm (chill) on the
'C' scale.