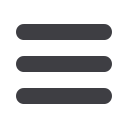
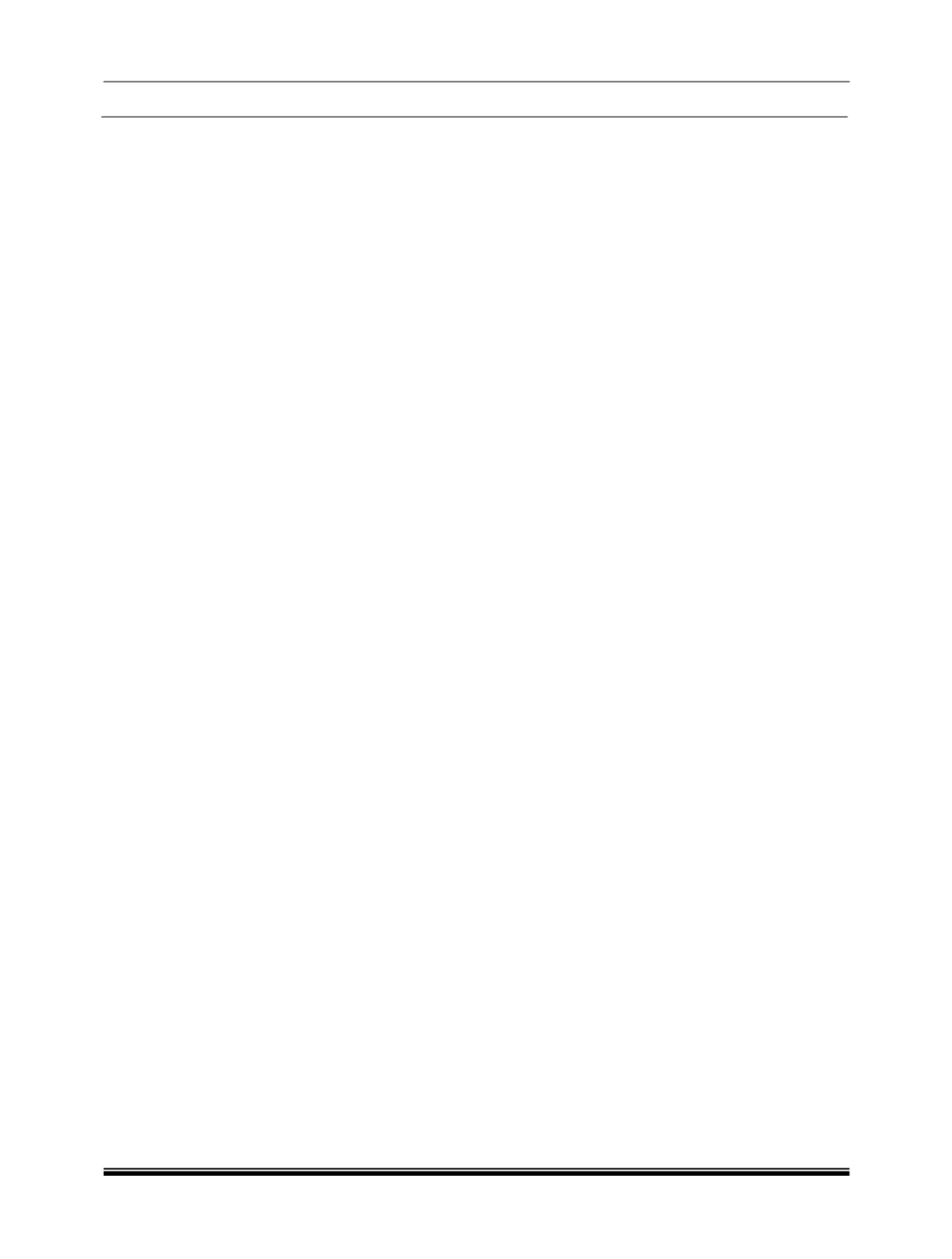
1.05L REVOTORQ ENGINE
45
Connect compression tester to adapter
and tighten vent knob.
Crank the engine with starter motor by
200-250
rpm approximately. Pressure
gauge needle will start rising. Continue
cranking till gauge needle stops rising any
further. Note down the reading. Loosen
vent knob to make sure the tester needle
returns to zero. Repeat this operation for
remaining cylinders.
Minimum compression pressure in each
cylinder should be
26 ± 1
bar.
Low compression pressure may be due to
leakage past valves / piston rings / blown
cylinder head gasket. To ascertain the
point of leakage, spray small quantity of
clean engine oil in to cylinder showing low
pressure. If it improves, wear in piston
rings / cylinder bore is indicated. If it does
not, leakage past the valves is indicated.
If compression pressure of adjacent
cylinder is also on lower side and equal, it
may be due to blown cylinder head
gasket.
d.
Fuel System
Check the Fuel system for fuel flow. If the
flow is restricted change the filter/ rectify the
defect.
e.
Clutch Slippage
Clutch slipping can be confirmed by any
of the following two methods:
Drive the vehicle with normal load in
3rd
gear
on level ground and let the speed
drop down to approximately
20 kmph
.
Now press accelerator pedal fully. With
slipping clutch the vehicle speed will not
pick up and also clutch burning smell will
be noticed. If this does not occur and
vehicle picks up speed, it indicates that
clutch does not slip.
f.
Brake Binding
During driving apply brakes number of
times and then shift gear to neutral
position and check free rolling of vehicle.
Check brake drums/brake discs for
overheating and if necessary jack up the
vehicle and check wheels for free rotation.
g.
Turbocharger :
Check for Tuning
1. Check intactness of actuator rod end.
2. Collapsed or restricted air pipe before
turbo
3. Check for crank bent or actuator rod
bend or hose pinch.
4. Restricted or damaged cross over
pipes turbo to inlet manifold
5. Foreign object between air cleaner and
turbo
6. Compressor./ Turbine Wheel damage
due to Foreign object entry
7. Turbine bolts, Compressor bolts,
actuator bracket bolts, or Clamps
loose.
8. Check Air filter for any blockage
9. Check for excessive back pressure.
If not OK the turbo charger must be
replaced.
Check Turbocharger compressor wheel
damage
1. Disconnect Compressor Air inlet
pipe.
2. Inspect compressor wheel blade.
3. There should be no visible damage.
If damaged, the turbo charger must
be replaced
The entire air circuit must be cleaned
or changed to avoid new failure in
case of foreign object
The foreign object can be found in
the heat exchanger
Check Turbocharger rotor movement
1. Check rotor movement, it should spin
freely.
2. There should be no trace of contact
with housing.
If not OK the turbo charger must be
replaced
Check Turbocharger Turbine wheel
damage
1. Disassemble
Turbocharger
or
exhaust gas connection.
2. Inspect turbine wheel rotor damage.
you need to look behind the blades,
damages are often located in tip area
If damaged, the turbo charger must
be replaced
The foreign object can be found in
the catalyst or in the particulate filter